ABOUT WPC
How to distinguish a quality WPC product
A large number of end consumers believe that all WPC decking boards are created equal, however a deeper dive reveals that this is not true. WPC profiles are produced from WPC granules, which in turn are made up of several components: wood, polymers and various additives. In the range of WPC boards available on the market, significant variations in quality have been found, which are determined by the type of components used, their ratio and the quality of each component. Currently, there are approximately 40 WPC board manufacturers on the European market, and the characteristics of their products differ significantly. In general, the principle applies – the lower the price and the product produced for a smaller market, the higher the probability that it will not contain all the necessary additives.
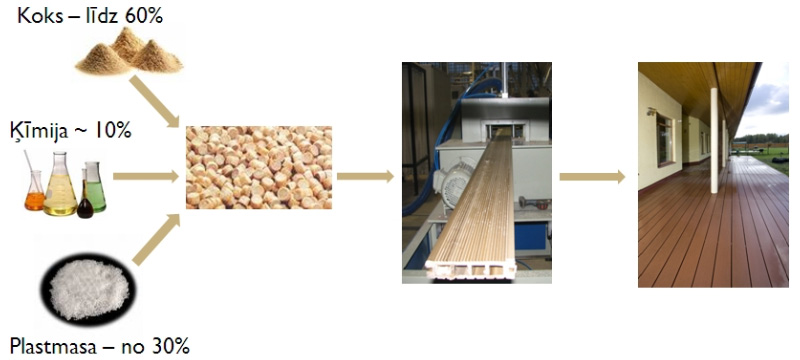
There are several categories where you can compare products from different manufacturers. As one of the main ones is the type of plastic used. 99% of the industry uses two variants – PVC (polyvinyl chloride) or Polyolefins (Polyethylene and Polypropylene). Better product hardness values are achieved using PVC, but the products are more brittle, which can be particularly well observed at lower temperatures. This nuance becomes especially important in northern countries, where the temperature is often minus degrees. Products containing PVC often do not enjoy a good reputation in the European market and are not considered particularly environmentally friendly, as there is a belief that PVC releases toxic substances over time. In contrast, polyolefins are widely used in the production of food packaging, tableware and other household products, which makes this plastic more attractive to consumers. There is no consensus on which is better, both types of products exist on the market, however, PVC-based products are mainly driven by large European manufacturers who have historically been involved in the production of PVC profiles (thus recycling waste produced by PVC factories into WPC products), while newly established companies usually chooses alternative options.
The wood used can be both wood shavings and dust, and its amount varies from 40 to 80%. In order for WPC decking boards to be suitable for outdoor conditions, or to be suitable for high humidity, it is necessary to ensure that the wood does not come into contact with moisture. This can be achieved by completely encapsulating each wood particle in a polymer shell. Using too little polymer and too much wood, the polymer shell is not fully formed, allowing wood particles to come into contact with each other, and moisture can travel inside the product, as a result, the board can swell, bend, rot. So the optimal ratio of wood and polymer must be achieved. If PVC is used as a polymer, the maximum amount of wood is up to 50%. When using HDPE or PP as a polymer, the optimally permissible wood composition is in the range of 50-60%, depending on the size of the wood particles and the ability of the equipment to mix the composition well. The wood preparation process is also important, because very fine grinds or wood dust serve only as a filler, while properly prepared wood fiber also fulfills a reinforcing function. As a result, it is possible to achieve much better physical parameters, however, the use of such fibers is up to several times more expensive and more complicated from the point of view of production.
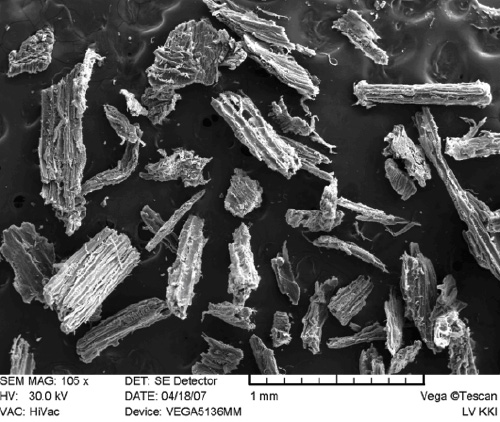
Unsanded WPC decking boards are also available on the market, with a declared wood content of over 70%, and the manufacturers position them as particularly ecological. The reality is that when sanding these boards, the only protective polymer coating is sanded away, but the exposed wood is susceptible to moisture. Therefore, the product will not be used outdoors. An additional problem lies in the fact that even when using an unsanded WPC board terrace, the boards will wear out over time, the unprotected wood will be exposed and moisture will damage the terrace. Usually, the desire of manufacturers to achieve high percentages of wood filling can be explained by the reduction of cost, however, it has been proven that at a wood concentration above 65%, the products begin to absorb water.
Additives such as color pigments, UV-stabilizers, fungicides, etc. are also used in production. Additives ensure and improve the mechanical properties of the product, prevent cracking, ensure color fastness, as well as resistance to fungi, mold, rodents, etc. All manufacturers consider this information a trade secret, and neither what additives are used nor their concentrations are disclosed. For very good products, even more than nine different additives may be used. It is also important to use additives in the necessary quantities, because without them, problems such as color fading and cracking due to UV rays, oxidation and many others can appear on the terrace boards. Unfortunately, these problems appear only in the long term, so the customer cannot determine the quality of the product in the store, and chasing after a cheaper product often leads to disappointment, for example, buying a cheap product made in Asia.
Products made in China also enter the European market, but they are of low quality. Research shows that many Asian manufacturers manipulate both the ingredients and their proportions. Produced only from recycled low-quality plastic. Using low-value chalk, talc and carbonate derivatives, the proportion of additives is increased up to 20%, thereby increasing the density of the product, but reducing other strength parameters. Other additives such as UV-stabilizers and fungicides are used less than intended or not at all. The most common wood-polymer ratio is 50/50 and bamboo powder is used instead of wood, because there are no wood fibers available in China that would provide a reinforcing effect to the products.
Unfortunately, it is difficult to visually determine the quality of WPC products, they mostly look good on the store shelf, but show their true nature only after installation. However, there are some points worth paying attention to before buying:
- Is the internal structure of the board straight – If the internal walls are not perfectly straight and do not form precise hollow chambers, this indicates a very poor quality product. There is a big risk that such a board will begin to deform over time.
- Are there any blisters in the material, or are pores exposed at the cut site – this is a sign that there was moisture in the material during the production process. Such material will also absorb water during operation and will deteriorate very quickly.
- Evenness of the surface – if you can see small differences in shades when carefully evaluating the quality of the surface, it means that the material is not evenly mixed, and most likely it will lack additives in some places, so it will also age differently. Even the smallest spotting will only intensify over time.